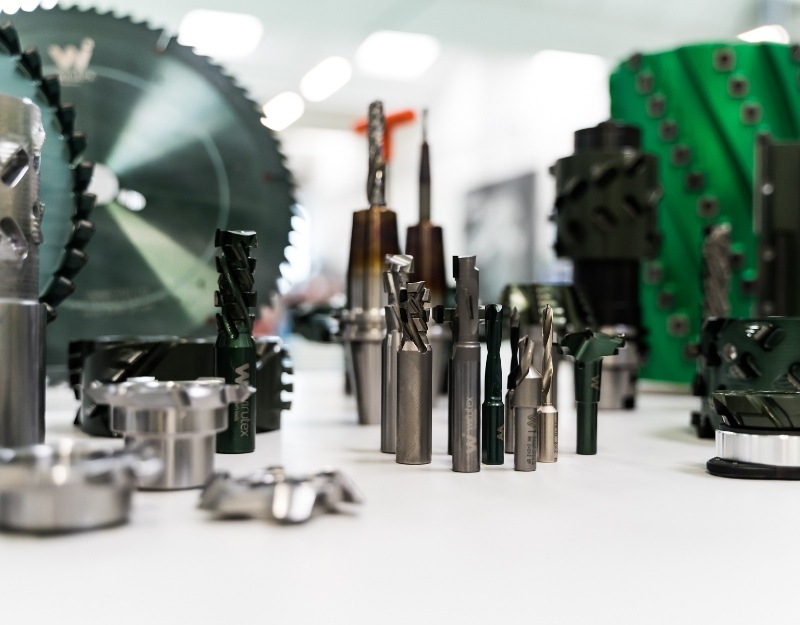
Diamond and carbide tools are the two categories of tools to choose from for woodworking cutters.The most frequently asked questions related to the choice of one or the other type of tool mainly concern the differences between the two materials in terms of price, characteristics, and intended use.
While it is true that polycrystalline diamond (PCD) tools have a higher purchase cost than the carbide version, it is equally true that, as we will see in a moment, the initial difference in expense is reabsorbed over time and is in any case justified by their specific characteristics.
Below we will go on to analyze the peculiarities of PCD and carbide cutters and provide useful suggestions for evaluating on what occasions and for what machining operations it is best to choose the polycrystalline diamond cutting edge and when it is better to opt for carbide instead.
First, however, an important premise must be made: the choice of tools can be influenced by many variables, some related to specific machining operations, others to the needs of the individual user. That is why it is always recommended to turn to experienced suppliers who can provide valuable support in choosing the most suitable type.
- What is polycrystalline diamond (PCD)?
- What is carbide (HW)?
- PCD vs. carbide diamond tools, costs and benefits
- Why choose Wirutex hi-tech tools?
What is polycrystalline diamond (PCD)?
Polycrystalline diamond is a composite material consisting of diamond particles sintered with a metallic binder.
The extreme hardness of diamond comes from a very compact, cubic crystal structure consisting solely of small carbon atoms arranged in a tetrahedral form that make strong bonds with all adjacent atoms.
From the early 1800s, that is, after the discovery that diamond was composed of pure carbon, and for more than a century, numerous attempts were put in place to reproduce the extreme conditions to create synthetic diamonds, but it was not until around 1940 that the first industrial diamonds appeared, by General Electric.
GE subjected Graphite (the other crystalline form of Carbon with a hexagonal structure) to temperatures of 2-3000°C and pressures of 50-100,000 bar, using catalysts of Nickel, Iron and Cobalt. In the 1970s, again General Electric originated CBN and later Polycrystalline Diamond (PCD) and Polycrystalline CBN (PCBN).
Since then its application has grown exponentially to establish itself as one of the most versatile materials in the woodworking industry.
The natural hardness of polycrystalline diamond has made it an excellent cutting material, ideal for making milling, sectioning and drilling tools.
When and why choose PCD tools
Polycrystalline diamond tools are distinguished by their very high hardness, which makes them extremely wear-resistant. Because of this characteristic, they offer longer cutting life than other materials. They also exhibit low friction during use, which promotes excellent finishes in cutting work.
Given their exceptional ability to withstand high levels of wear, PCD tools are valuable allies in machining all those abrasive composite materials that are sometimes difficult to machine with carbide.
They are best used on materials such as chipboard and laminates, as well as on:
- MDF/HDF;
- phenolic;
- fiberglass;
- carbon fiber;
- PVC;
- Corian;
- HPL.
The use of diamond tools on ferrous materials, however, is not recommended.
If you are inclined to purchase a polycrystalline diamond tool, it is important to talk to the manufacturer, discuss in detail the use to be made of it and what the machining expectations are.
Indeed, it is not enough to buy a PCD tool to be guaranteed a good result. One must also know how to use it!
This is what the comparison with the manufacturer is for: relating the specific characteristics of the PCD cutter, blade or bit to the material to be machined and the type of machining to be done.
Based on this information, the supplier will know how to recommend:
- The most suitable PCD grit size;
- the optimal tool geometry.
These evaluations are important not only to achieve the best possible result, but also to optimize the purchase cost of the diamond tool.
What is carbide (HW)?
Belonging to the category of cermets, Hard Metal (also known as Widia) is a material consisting of hard particles, most frequently Tungsten Carbide, embedded in a metal matrix (often cobalt), which combines hardness and wear resistance with resistance to crack propagation.
It was Germans Karl Schroeter and Heinrich Baumhauer in 1923 who first sintered Hard Metal at the Osram Lamp Company in an attempt to produce a material capable of cutting tungsten into thin filaments for insertion into lamps. Friedrich Krupp acquired the patent for this process, and in 1926 his company began producing the material, which came to be known as Widia (from the German "Wie Diamant").
In 1928 the American General Electric acquired the rights to produce the material in the U.S. where it took the name Carboloy.
Carbide tools, when and why to use them
Carbide or carbide tools tend to wear slower than steel tools and can withstand higher temperatures.
Carbide tools are characterized by high wear resistance and high toughness, and are recommended for machining materials that require more chip discharge, such as hardwoods.
In addition, they are effectively used in machining operations where, during the same day, the tool is processing different types of material, and in those where a high quality of finish is not required: the cutting edge of carbide tools, in fact, deteriorates from the earliest stages of cutting.
PCD vs. carbide diamond tools, costs and benefits
In addition to technical considerations, the choice between polycrystalline diamond and carbide tools is often influenced by cost.
As mentioned, carbide tools have a lower purchase cost than polycrystalline diamond tools. But are we sure that this represents real savings in total production costs?
To answer this question, we cannot help but once again relate the "purchase cost" factor to the actual benefits and advantages we can gain by opting for one or the other solution.
While carbide cutters and drills are more advantageous considering the initial sum to be invested, polycrystalline diamond tools for some companies may prove more beneficial in the long run.
Although at first glance PCD tools are more expensive, when we calculate the cost per linear meter machined, with the correct application, diamond tooling will prove to be a wise choice and an investment that pays for itself rather quickly.
In fact, diamond blades, cutters, and tools not only offer high performance in cutting applications, but are also able to significantly reduce a company's overall costs under the heading of "tools". Costs that can be further reduced by proper use and maintenance.
After careful calculation, it emerges that the cost of a polycrystalline diamond tool is only one-fifth of what the equivalent of a carbide tool would cost, since already from the first life cycle PCD tools can reduce costs by 30-50% compared to carbide or insert tools.
Not all companies, however, need to use diamond tools. In fact, it is important not to fall into the reverse error: if the company carries out machining on different types of materials more frequently, PCD cutters are not always advisable.
Thus, the cost-benefit analysis must always be contextualized to the type of business being conducted and the machining being done most frequently.
How to recognize the most suitable tools?
As noted above, it is essential to know in detail the characteristics of the tools on the market. In fact, in-depth knowledge of the product makes it possible to evaluate it correctly and minimize the risk of error.
In this sense, it is vitally important to rely on professionals in the field, the only ones able to guide the customer toward the most suitable solution, after relating the different variables: material to be machined, type of machining, needs and expectations of the user.
PCD cutters, for example, are not highly recommended in cases where the main need is to work on all materials.
Therefore, before purchasing the tool, one should ask oneself: how many times will I be able to sharpen this tool? how much will it cost me to sharpen it? how long will it take me to assemble/disassemble and reset the machine during sharpening?
These questions can be answered by looking at the main differences between diamond and carbide tools on an item-by-item basis:
- Cutting life: Diamond tools have an average cutting life 50 times longer than carbide tools (data that may vary depending on material processed, speed, etc.);
- Cutting quality: Both diamond and carbide initially offer excellent cutting quality; however, carbide deteriorates from the earliest stages of cutting, while diamond quality remains unchanged until the first sharpening;
- Re-sharpening: Carbide tools need to be re-sharpened more frequently than diamond.
Having to resharpen a tool also means more machine downtime, longer time for machine resetting, and the need for more replacement tools.
Find the ideal toolmaker for the right job
As we have seen, in order to correctly choose the right tool material for one's needs, one must consider a number of elements such as the type of material to be machined, the composition of the batch being machined, the finish of the machining required, and a cost analysis.
An error in evaluation could prove detrimental to the production process both in terms of machining quality and operating costs.
For this very reason, it is a good idea for the customer to rely on a tool manufacturer who can direct him to the products that are best suited to him.
Why choose Wirutex hi-tech tools?
Wirutex hi-tech tools is the ideal company for those who want to rely on a technology partner with extensive experience gained in the field.
Its wide range of high quality polycrystalline diamond and carbide tools is the result of continuous investment in innovative technologies, which enable state-of-the-art design, development and production processes.
Wirutex hi-tech tools manufactures and distributes:
Whatever the choice of tool-diamond or carbide-it is essential to know how to use it properly: even the best tool on the market will not perform to its full potential if it is not used according to established parameters.
This is why it is important to seek the advice of an experienced tool manufacturer who can provide the guidance to achieve an optimal balance between the various machining parameters.
If you have any questions regarding which cutting material is best suited to your machining requirements, please contact us by clicking here.